I have been experimenting with a few ideas while waiting for epoxy to cure between rounds of finish work on the cabin top and doors.
My airplane will be IFR capable and I will be installing an alternate static source valve. Many builders use a Clippard TV-2SP pneumatic valve that actuates like a toggle switch. After getting the valve, I noticed that it moves very easily from the closed to the open position.
I then became curious to see if I could find a way to detect the position of the valve to use as a discrete input on my EFIS. On inspection, I noticed that the base of the poppet valve stem is visible via the inlet port. The stem moves about 3/32″ of an inch from the open to the closed position. This provides the possibility of sensing the status of the valve by detecting the position of the stem.
I designed a 3d printed part to house a limit switch that could be threaded onto the inlet port of the valve. A 3d printed insert is press-fit and glued into the housing to guide a probe. The air flows around this insert.
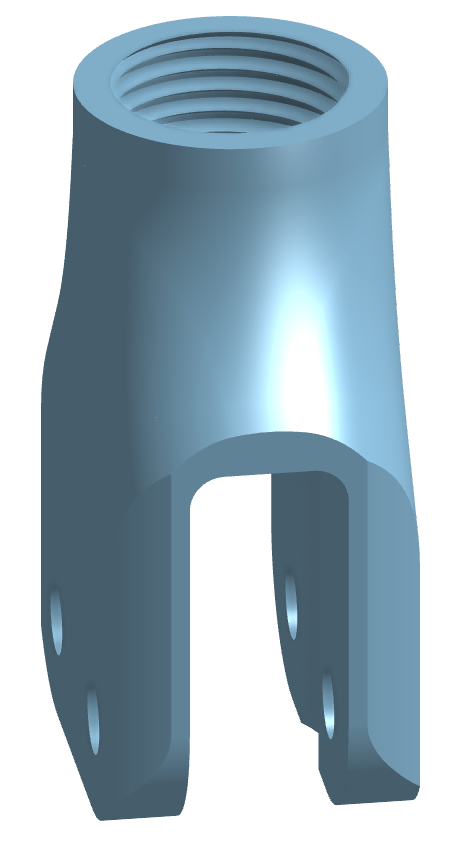
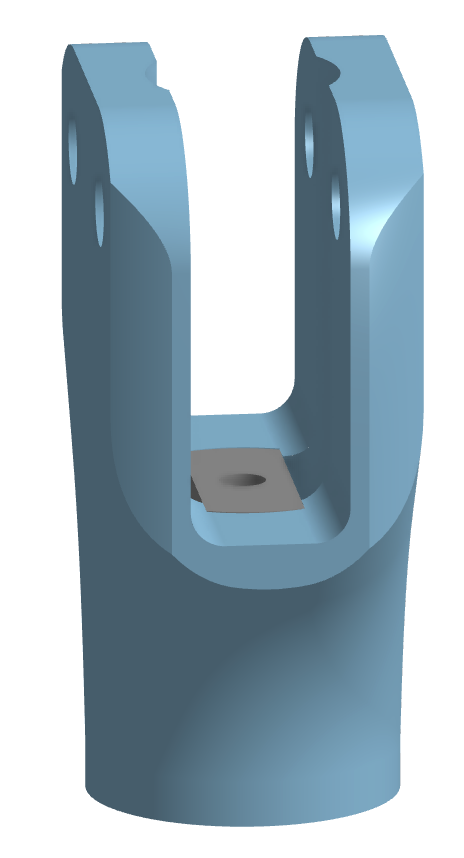
I used the mandrel from a pull rivet as the probe. The rounded head of the mandrel provides a smooth contact surface to rest against the base of the stem. Pressing on the probe closes the limit switch. I designed the housing around one of these limit switches (with the roller removed).
I used #4 stainless screws to attach the limit switch as they thread snugly into the mounting holes on the switch.
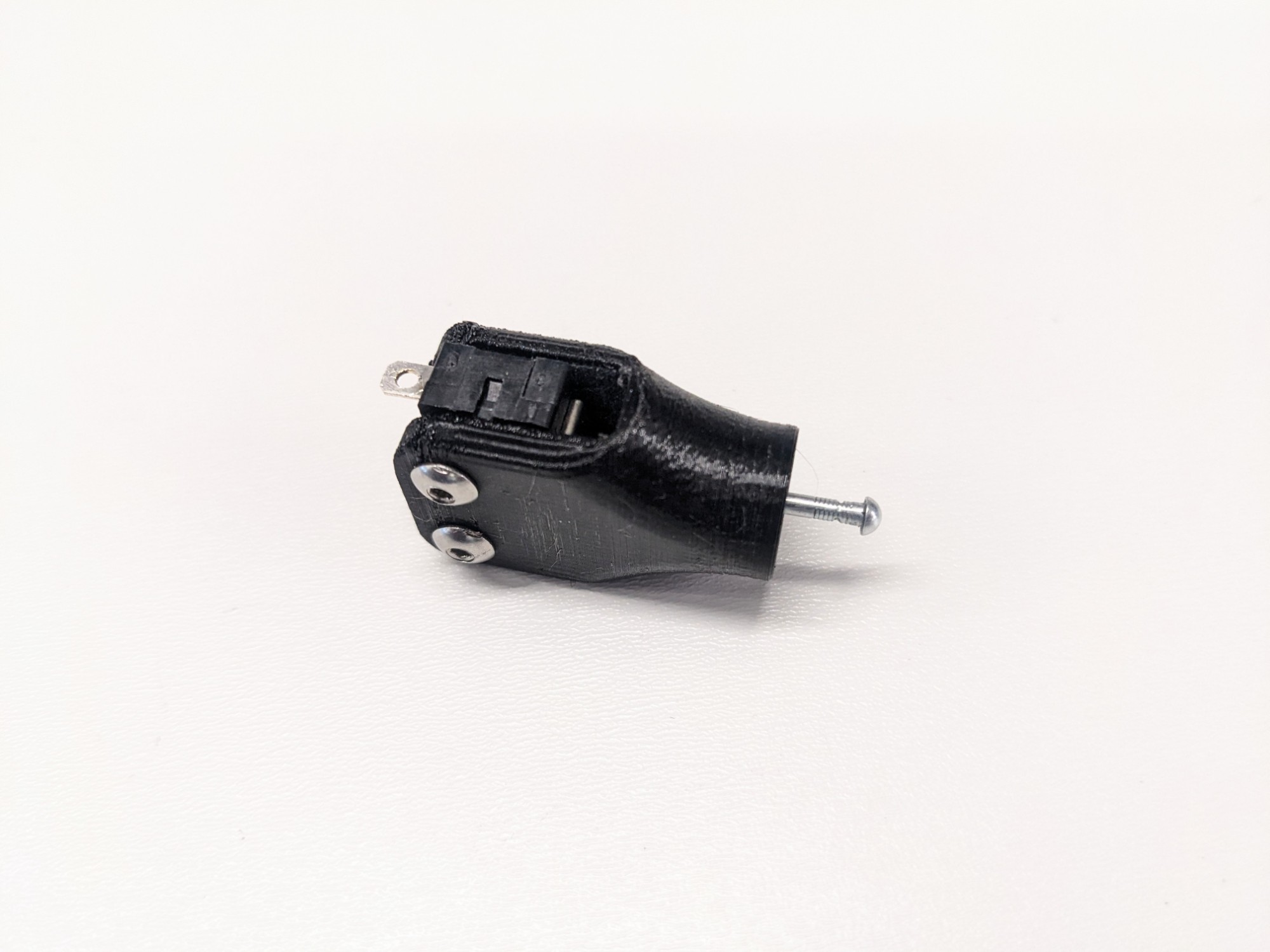
The outlet port has a #10-32 thread. I purchased an elbow to adapt the port to a 1/4″ push-to-connect fitting which I will tee into the static line.
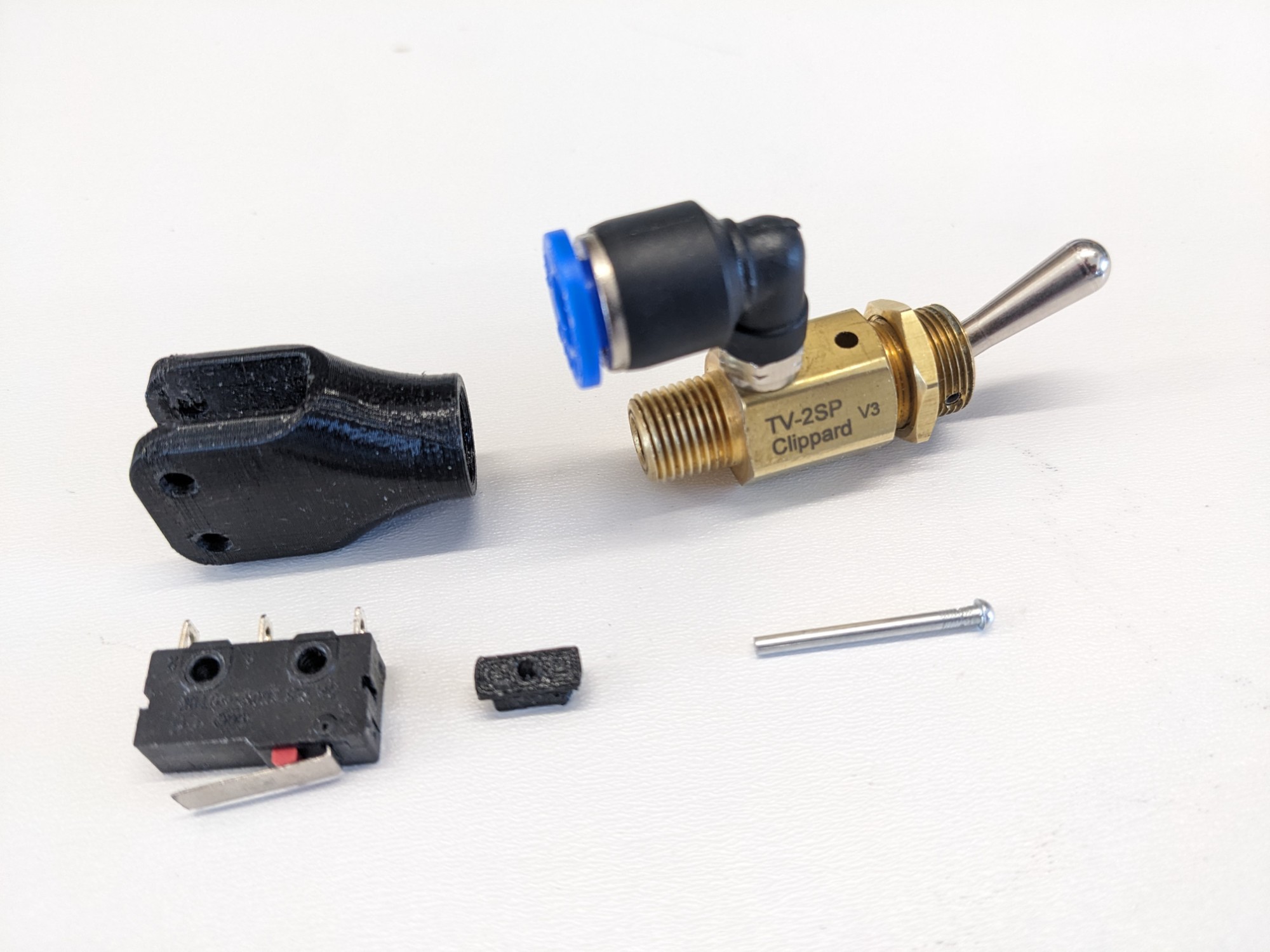
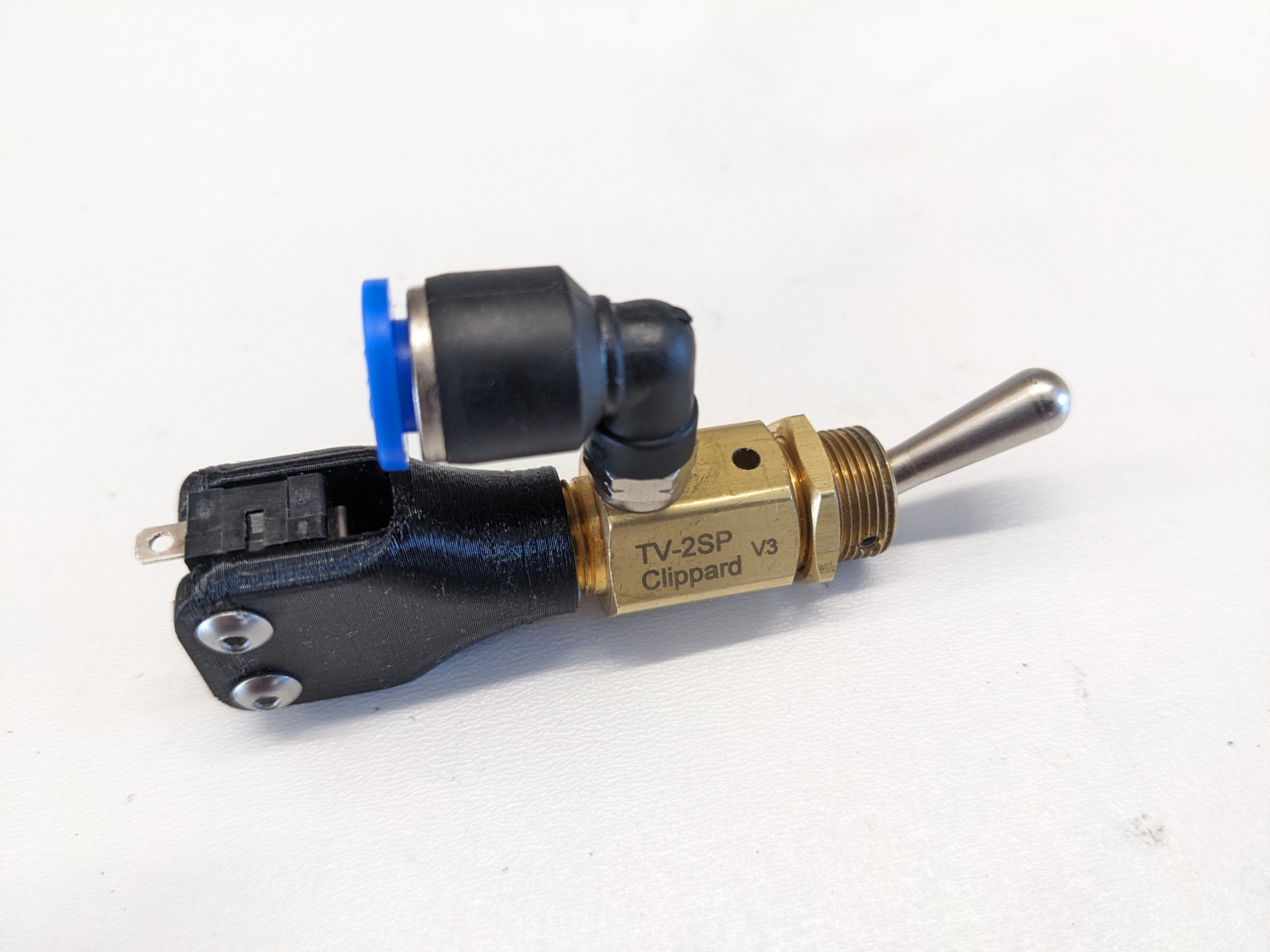
Success. I’ll use this to trigger a caution CAS message on my EFIS.
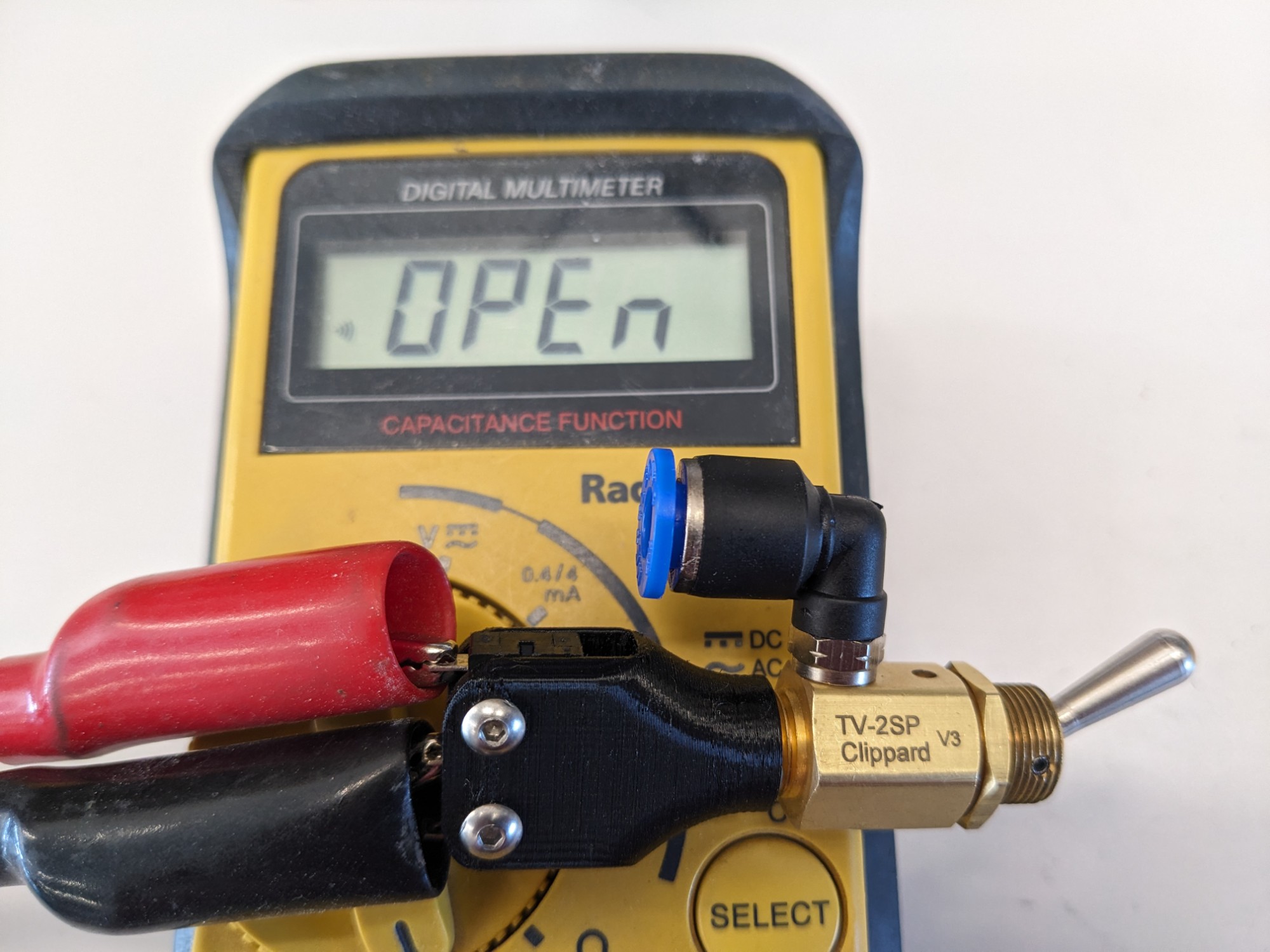
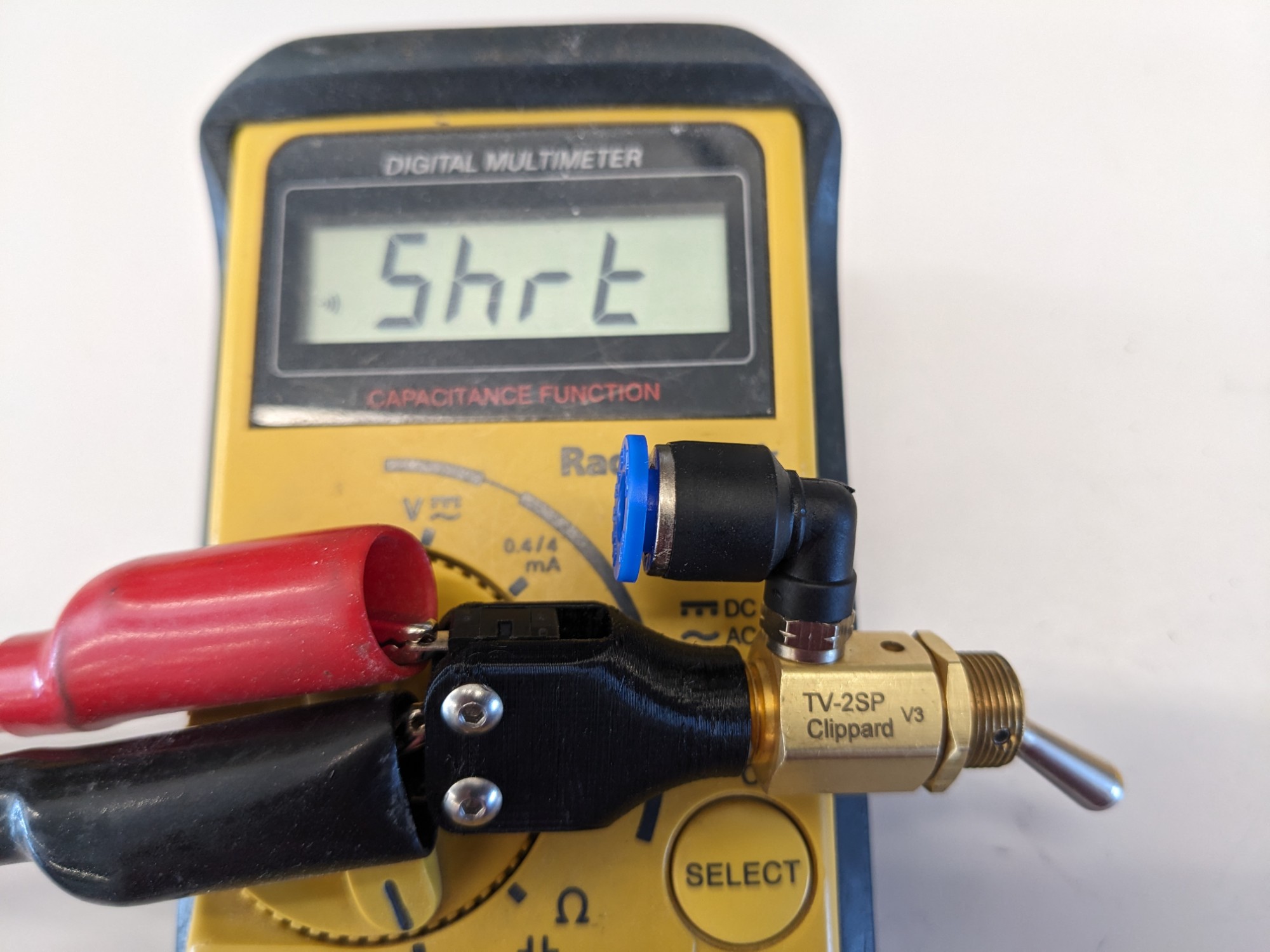