I took the opportunity to attend the Avionics Installation for Experimental Aircraft course at the Aircraft Electronics Association (AEA) headquarters in Lee’s Summit, Missouri. This is a 3-day course that focuses on the Garmin G3X system.
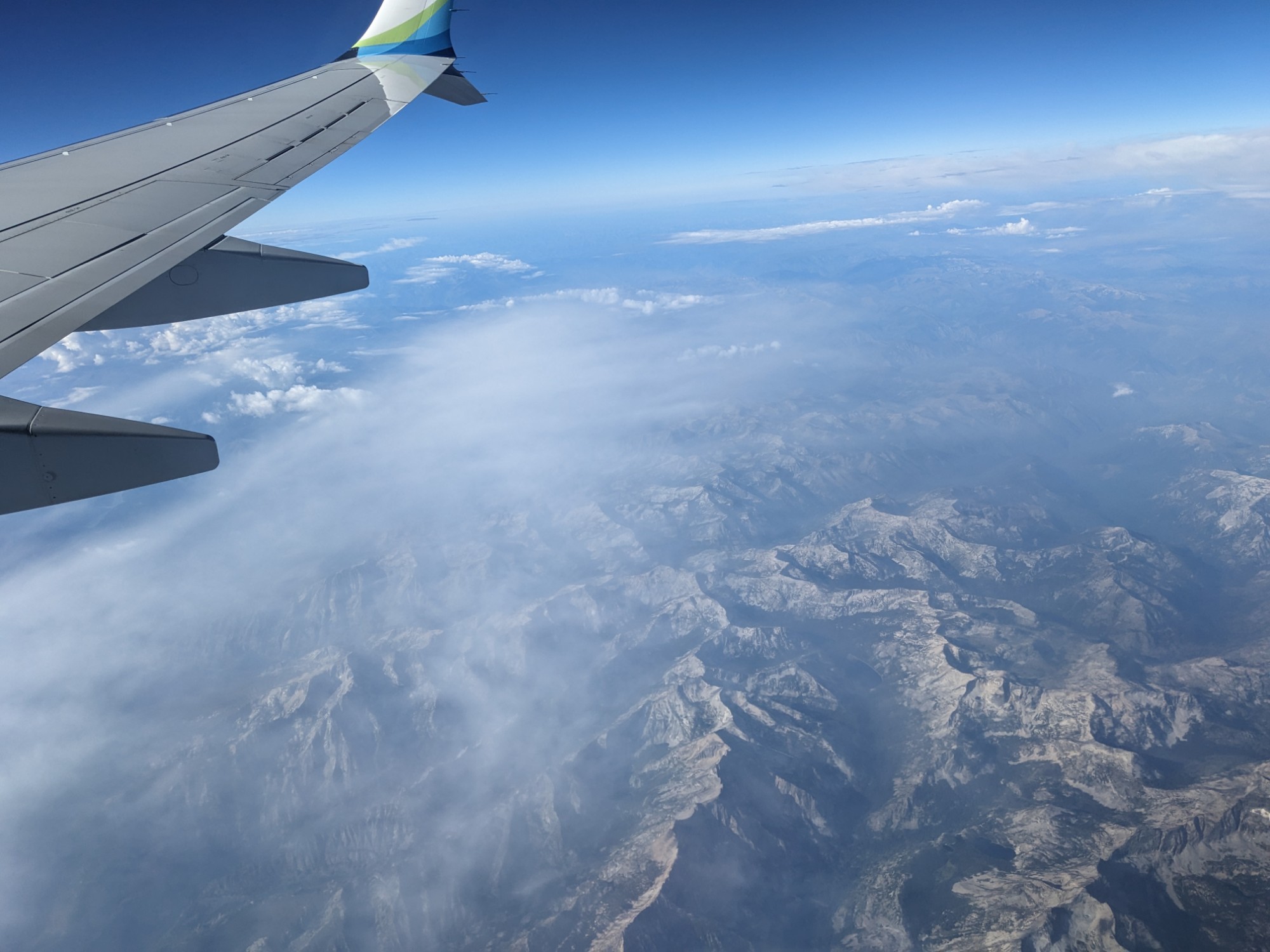
I arrived Sunday afternoon and stopped by the Lee’s Summit airport (LXT) while exploring the area.
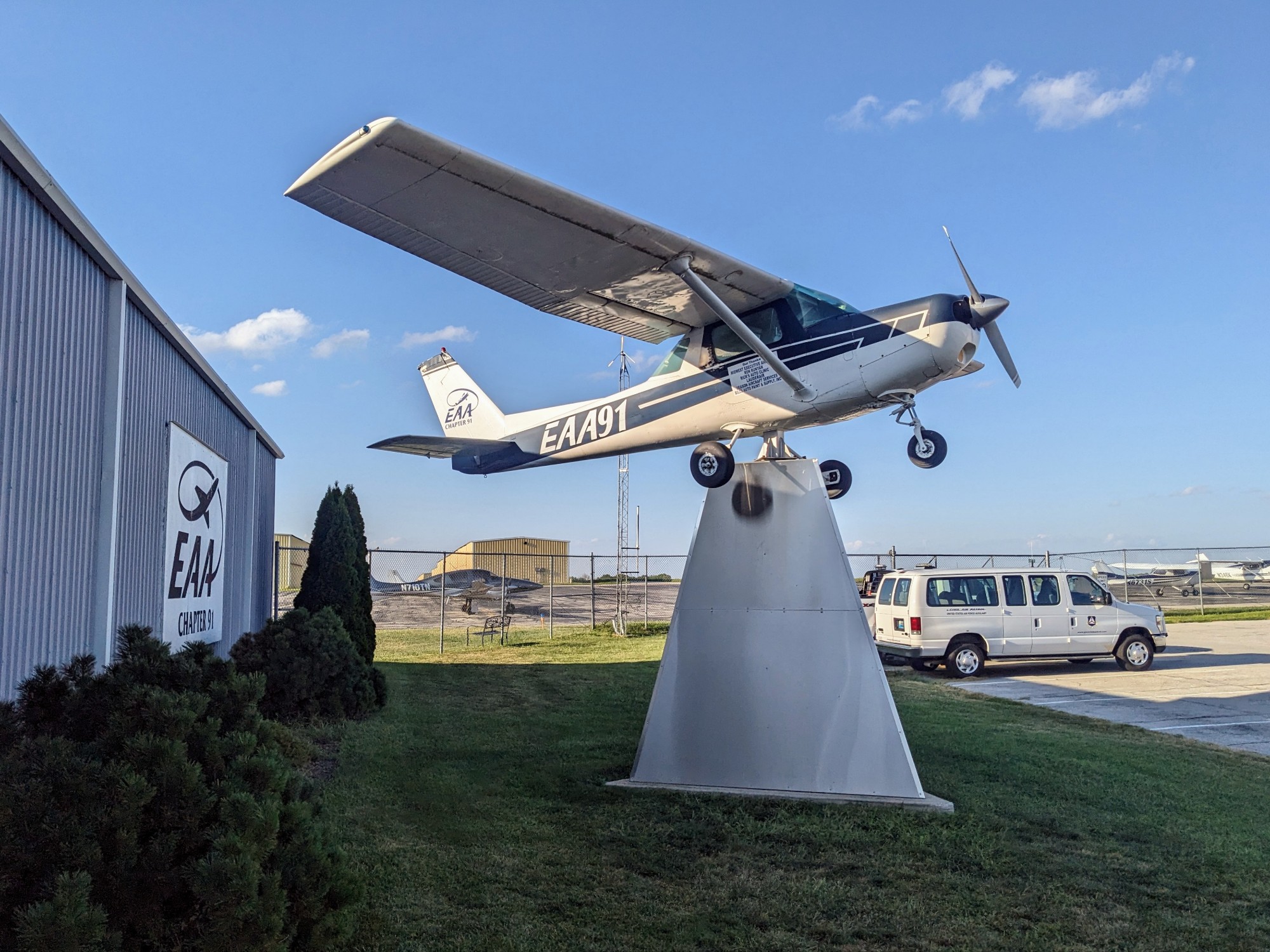
The AEA office is located to the northeast of the airport and is not on the airport property.
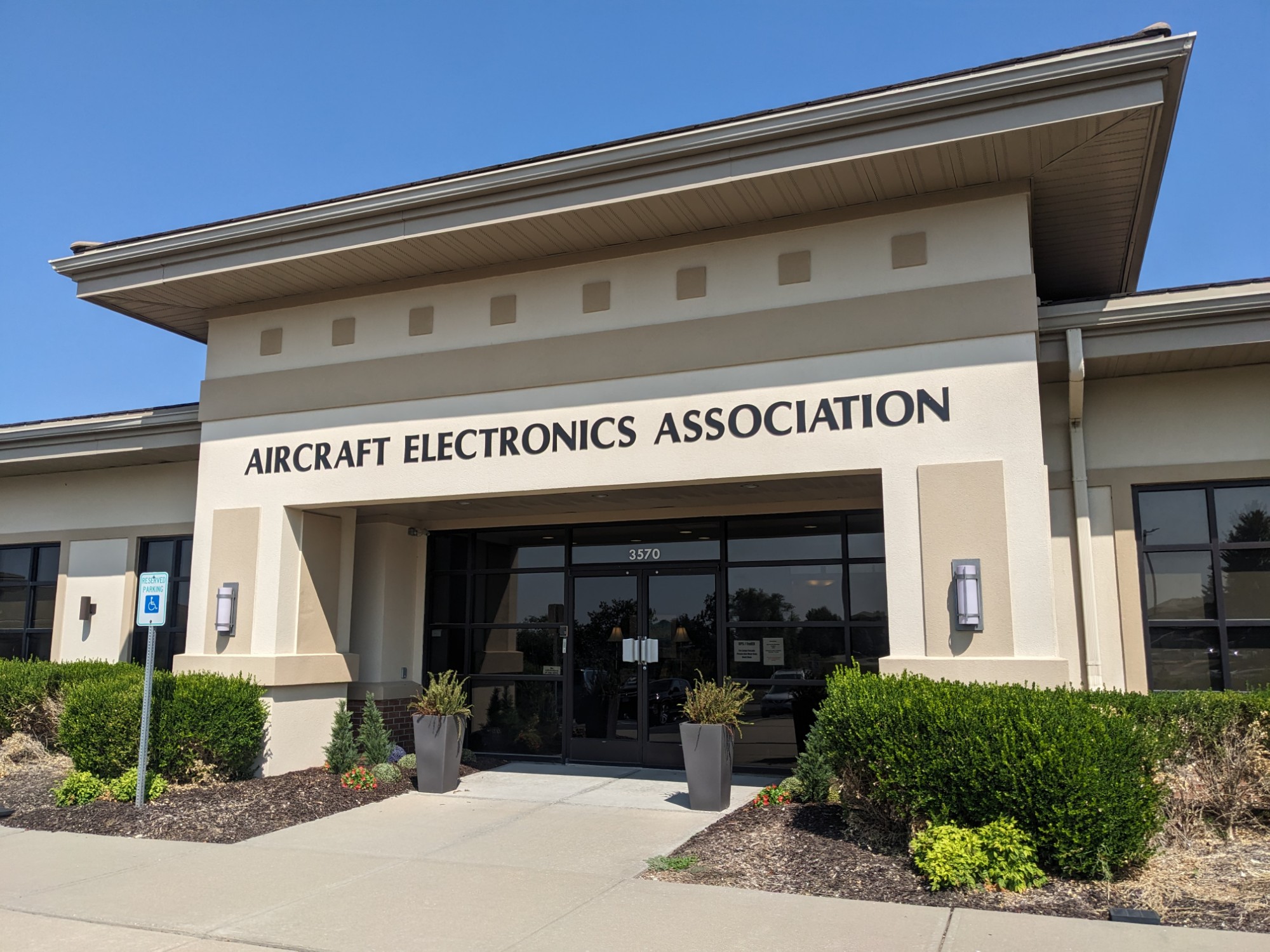
The course steps though the planning, installation, interfacing, configuration, and troubleshooting of a G3X system. The course material was very well done and will be a really useful reference as I work through the design and installation of my avionics.
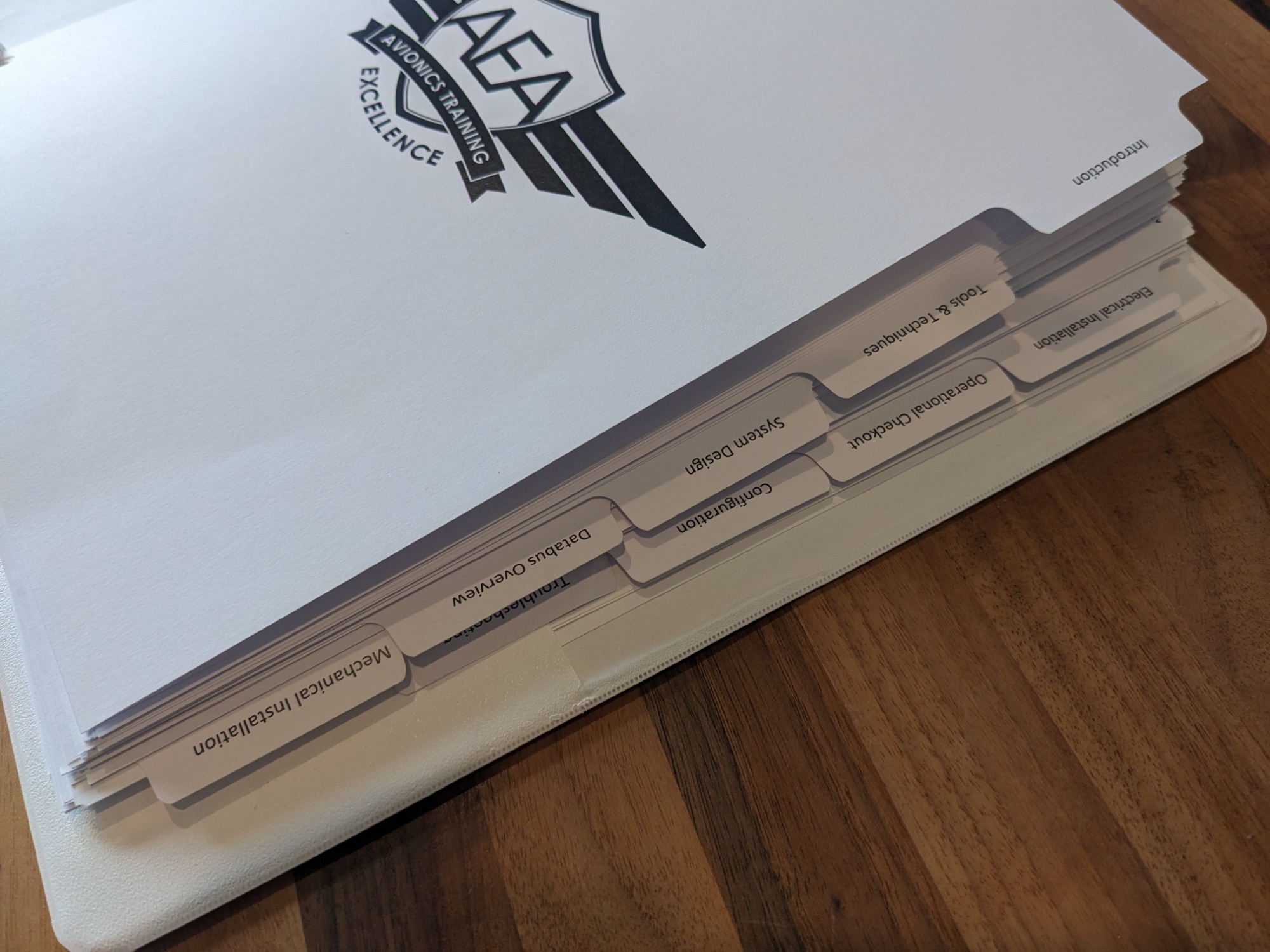
A significant portion of the course involves the hands-on construction of a wiring harness for a simple G3X system (which includes a GDU 460, a GMU 11, a GSU 25, and a G5).
I found this portion of the course to be particularly valuable, especially combined with the many real-world insights provided by the instructor (Levi Self, founder of Midwest Avionics, and former Garmin employee).
The instructor-led course material is scheduled for the morning portion of the day and the hands-on work occurs in the afternoon. Many in the class had their harnesses completed by end of the second day. Time was made available on the third day if needed to complete the project.
All of the components needed to complete the project are provided including wire, solder, pins, terminals, labels, heat shrink, etc.
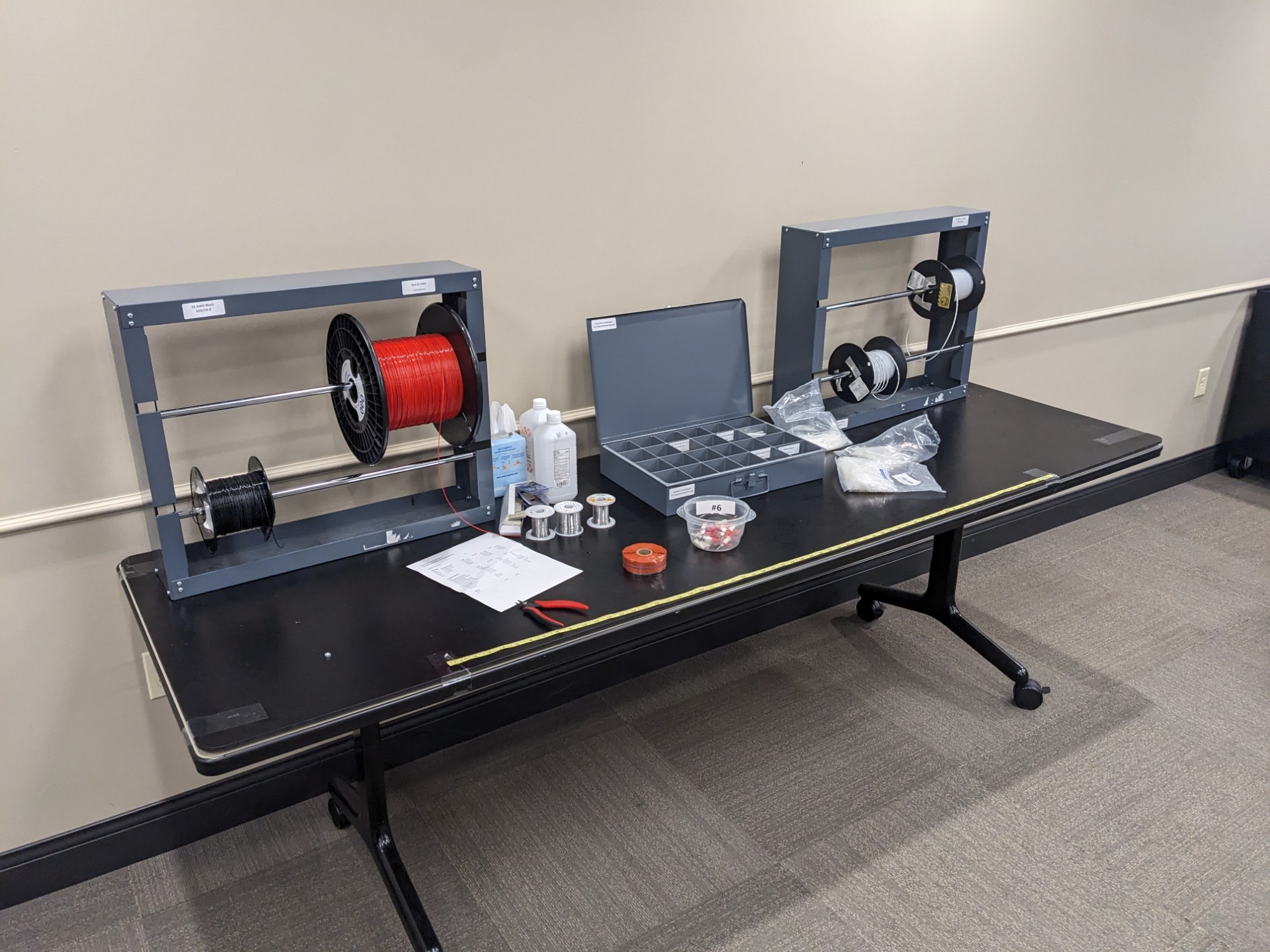
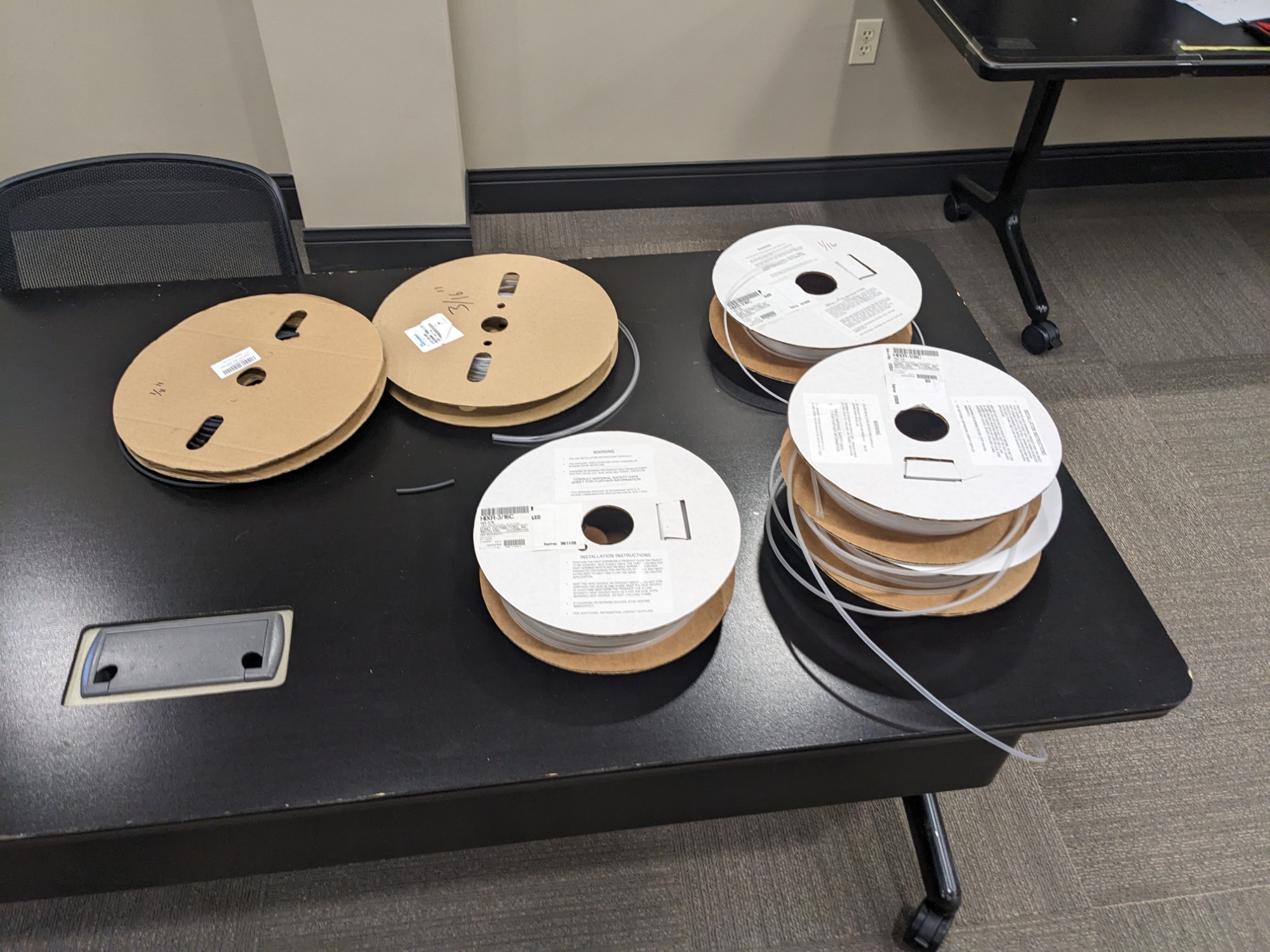
A tool chest is provided for each pair of students, with two of each of the frequently used tools so you don’t have to trade back and forth.
The hands-on work starts with laying out the dimensions of the harness on the table. After going through the course, it becomes very clear why this approach is recommended (vs. stringing wires one-by-one into the airplane). The result is a much cleaner and more maintainable install. Pre-planning is needed, but it becomes clear that the planning time will easily pay for itself. All of the repetitive work (running wires, labeling, stripping, splicing, pinning, etc.) can all be done comfortably without having to climb into the airplane and work in a restricted space. Everything ends up being labeled, documented, and maintainable. The instructor also shared a lot of tips and techniques for promoting future accessibility for the inevitable maintenance and upgrade tasks that will be needed.
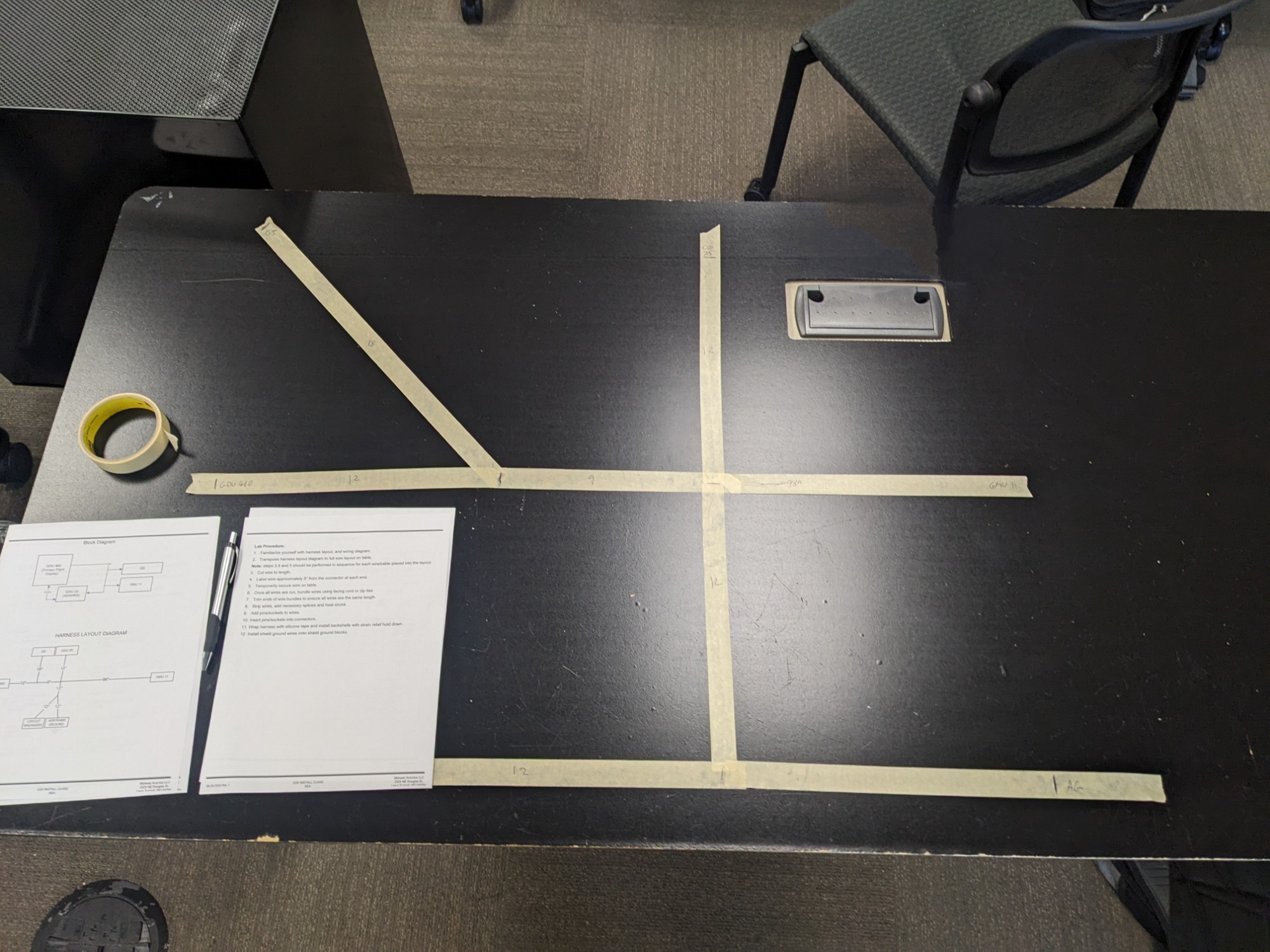
Wires are then added, labelled, and bundled. I chose to use wire lacing to do the bundling, but zip ties are also provided as an option.
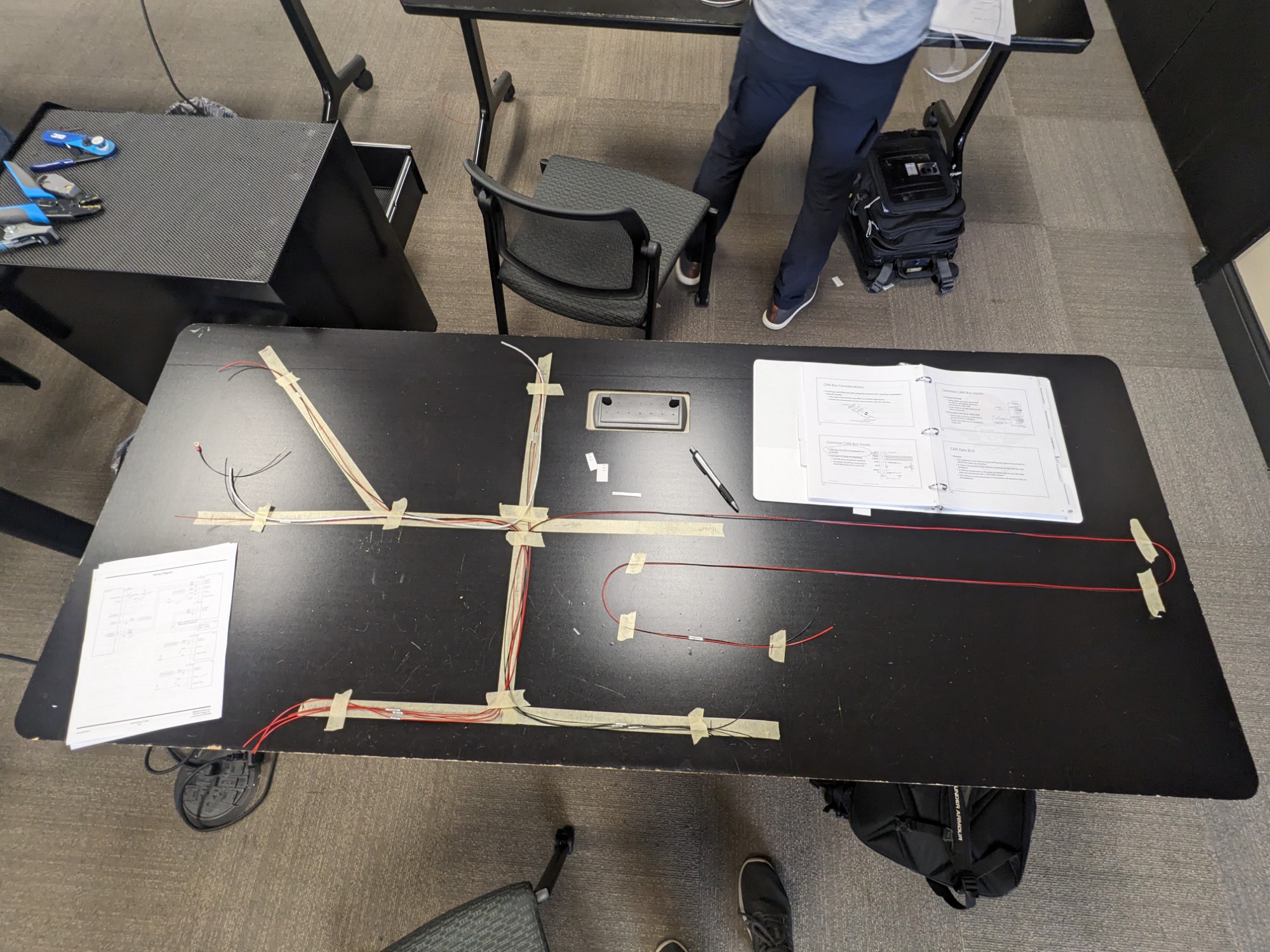
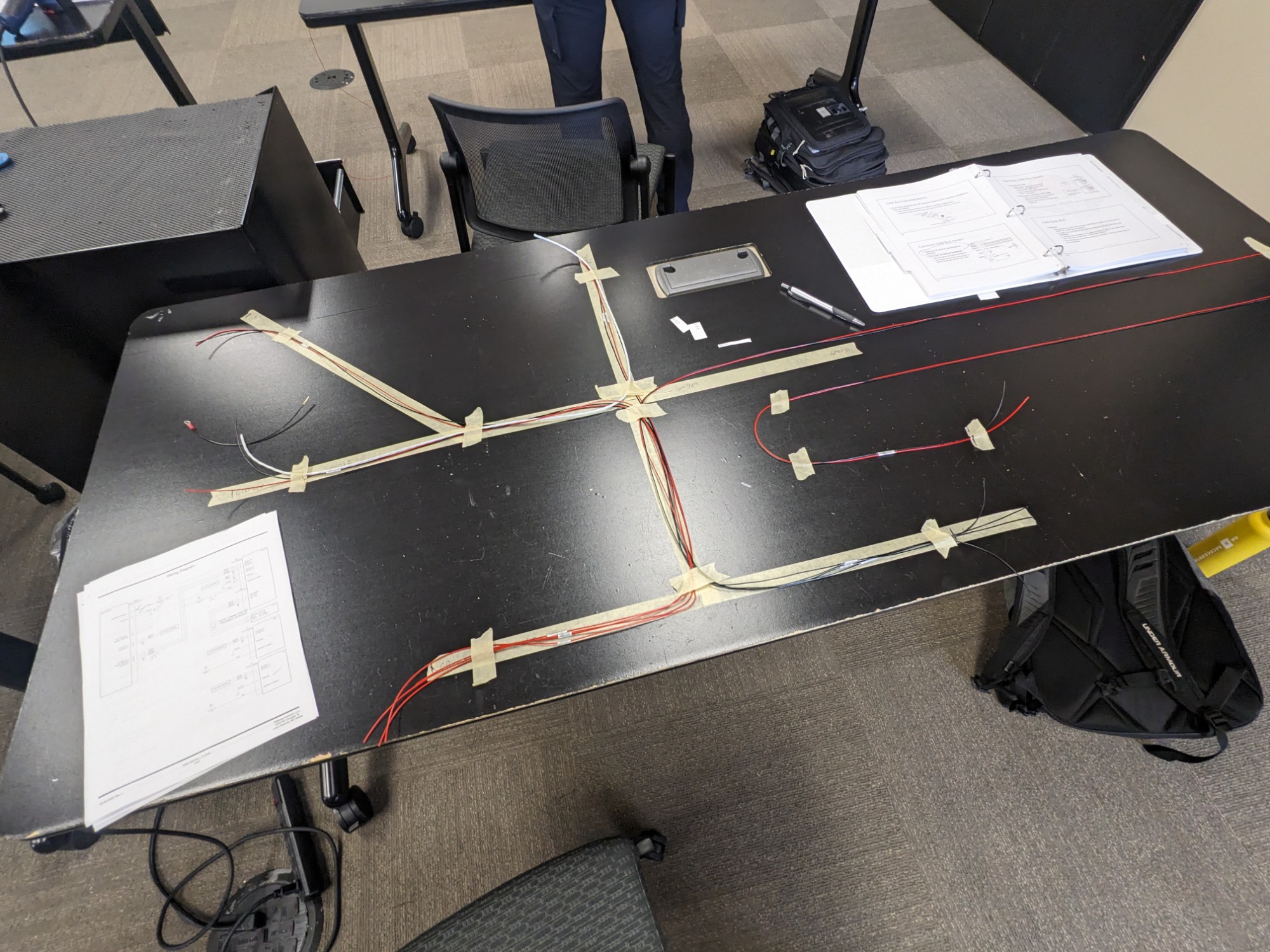
Instruction is provided for stripping wires and crimping pins and terminals. Instruction is provided on how to setup and use the tools. Tool purchasing recommendations are provided. Multiple techniques for grounding shielded wire are presented and practiced.
CAN bus planning and construction techniques are also described and practiced (shield termination, CAN termination, window splices, etc.). An RS-232 connection is also assembled (GDU to GSU). Additionally, two BNC connectors and a portion of RG-400 are provided for practicing the assembly of antenna cables.
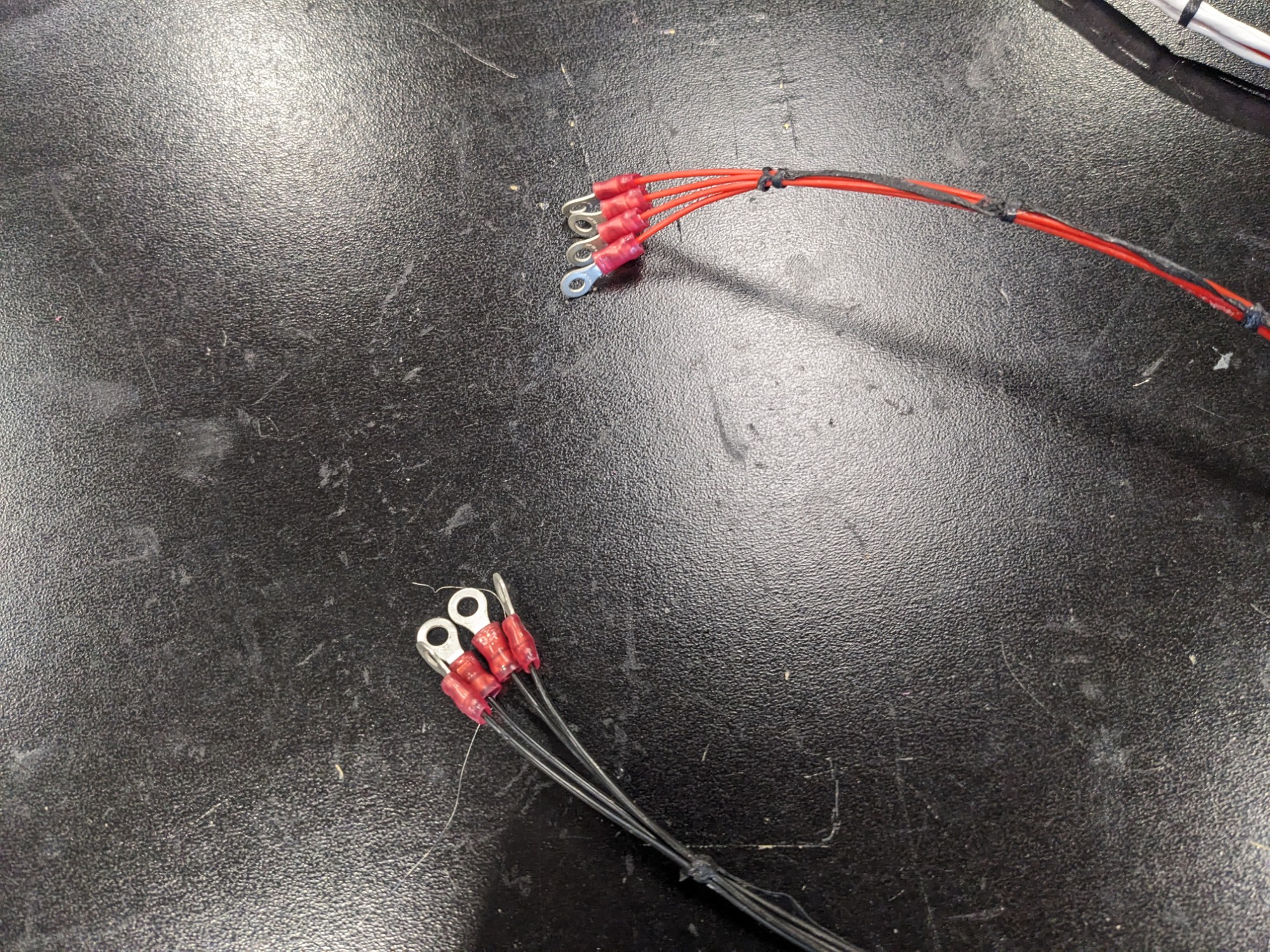
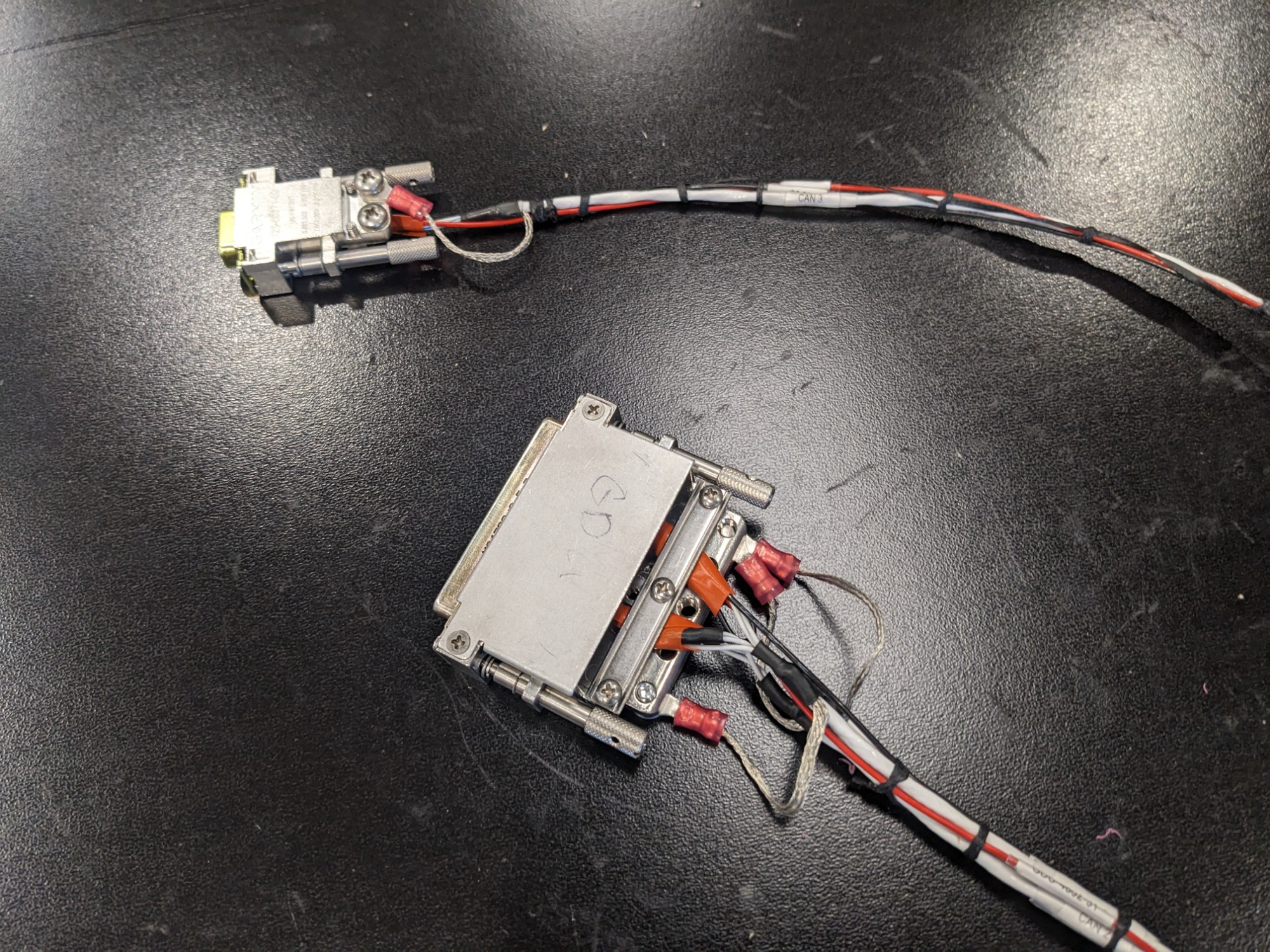
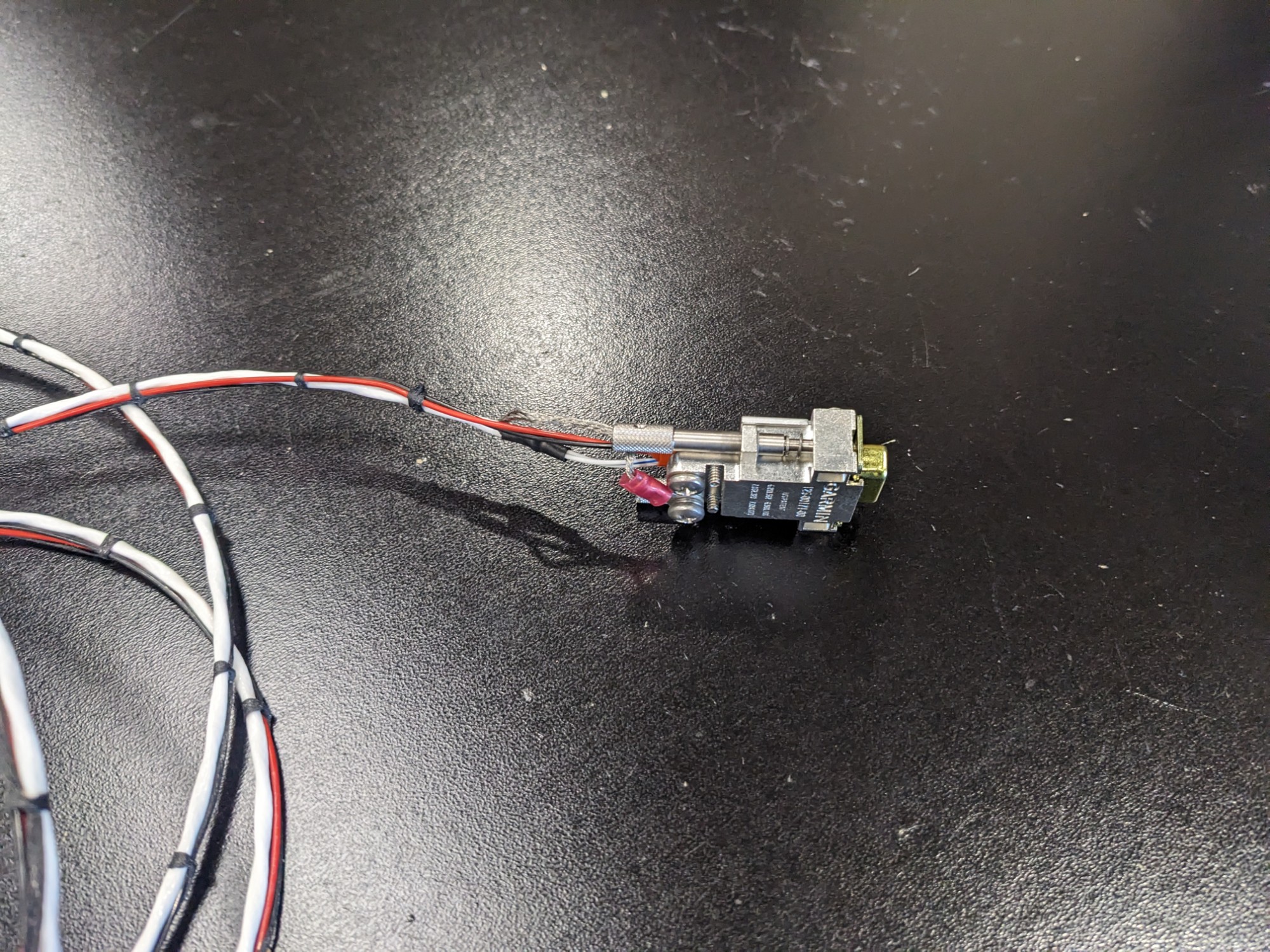
I completed my harness on the afternoon of day 2. It looks pretty simple but there is a surprising amount of work required to build out a harness. I came away with a lot of respect for how long this will take to plan and build out for my panel.

A test stand is provided for testing the completed harness.
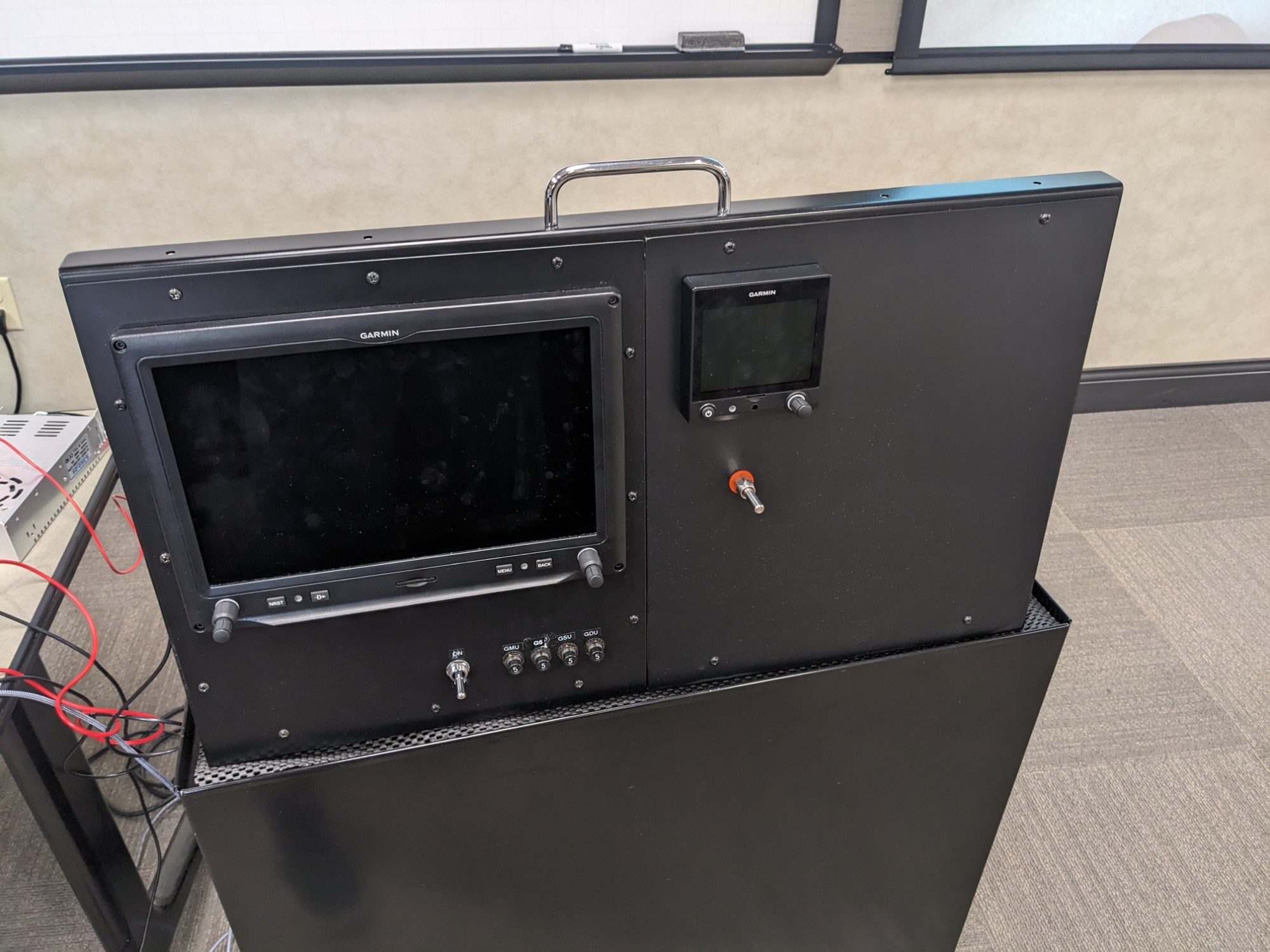
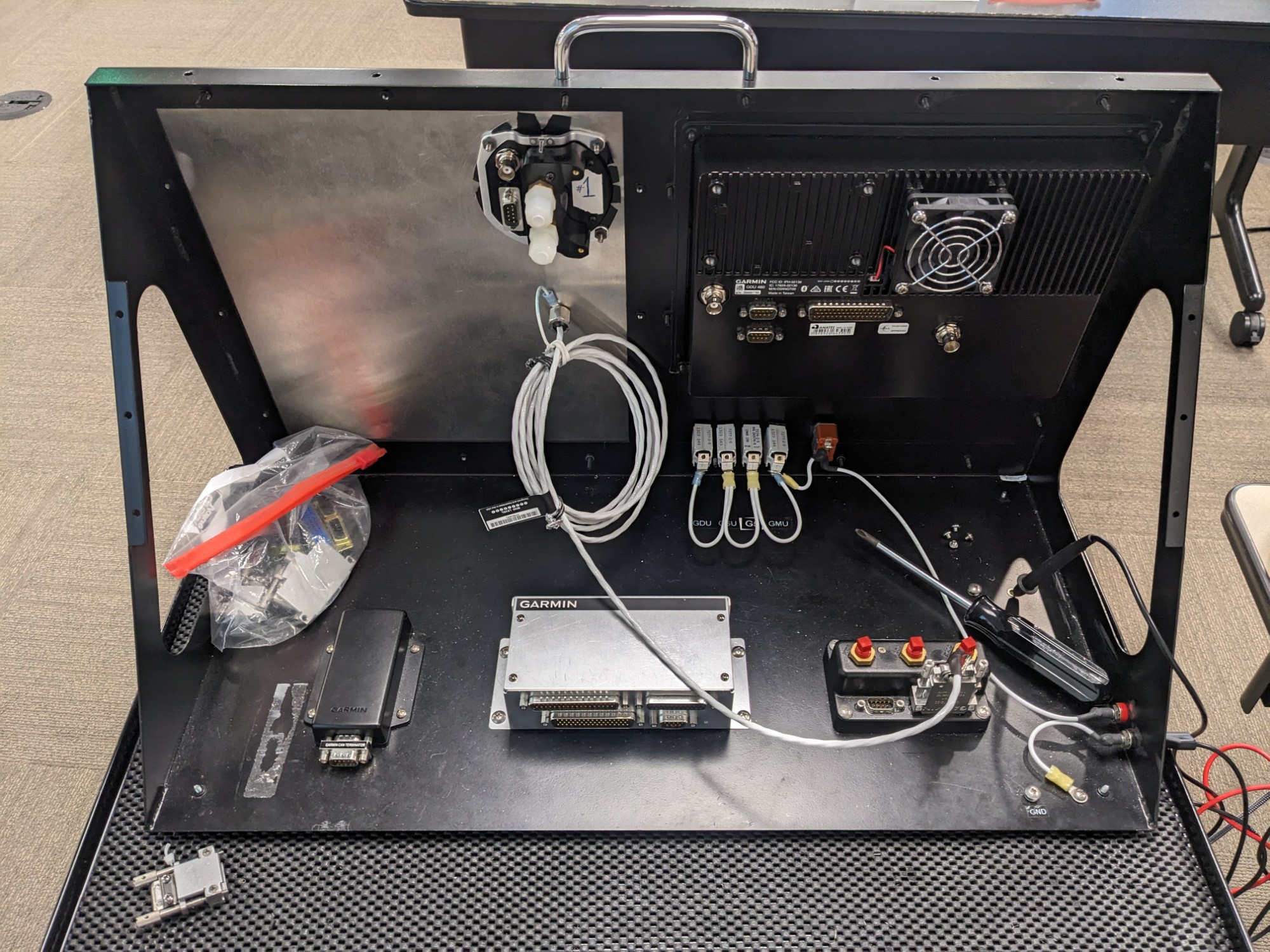
The harness is tested with a multimeter first (to sanity check ground and power connections) and is then connected to the test stand. If all goes well, the equipment starts up and the magic smoke stays in. The instructor then runs thought the basic steps required to check the configuration and to ensure that the CAN bus and RS-232 connections are working correctly.
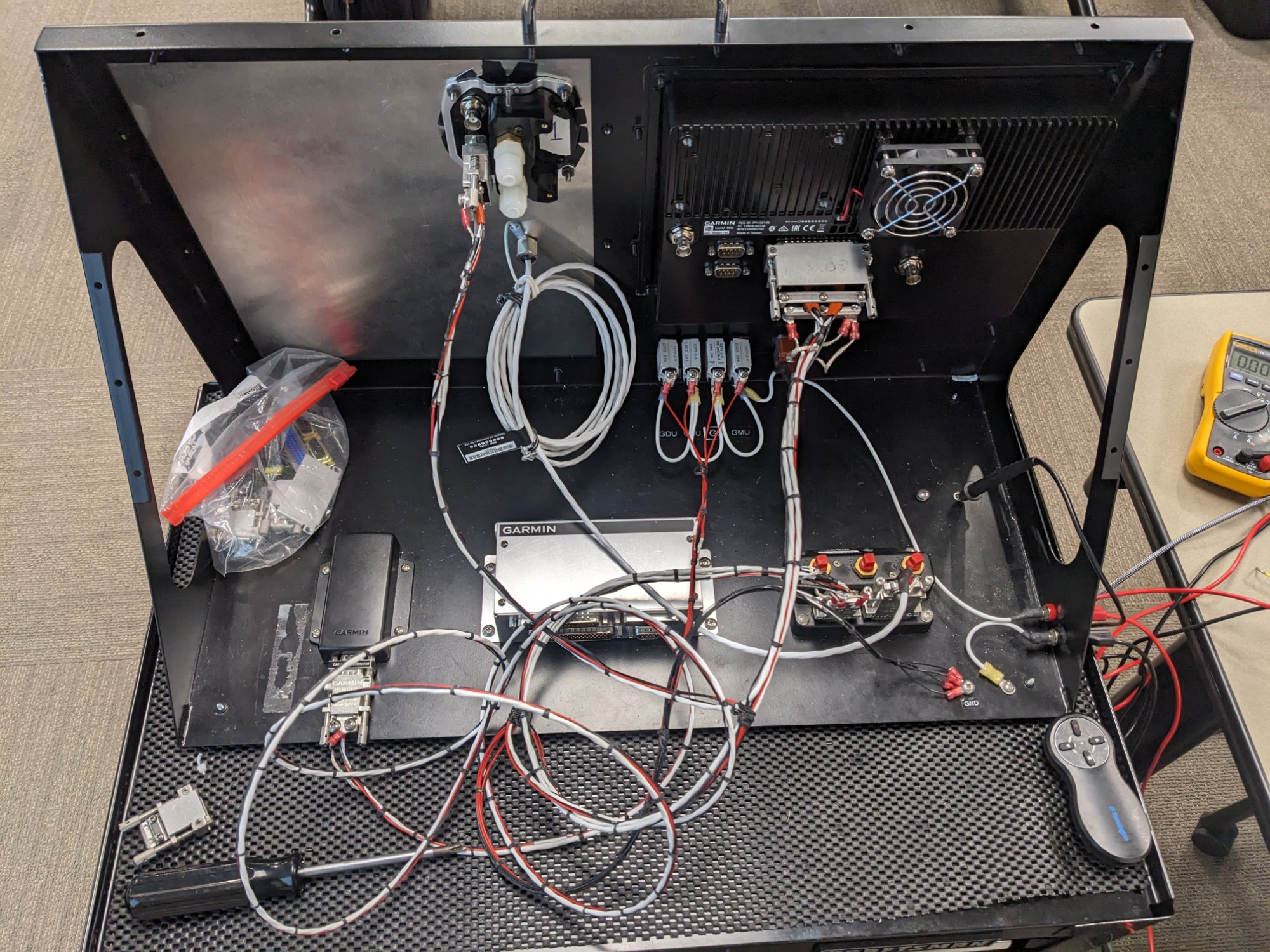
Having completed the training, I feel much more confident now in my ability to design and construct a high-quality harness for my airplane. While none of the techniques are particularly difficult, the opportunity to learn hands on was invaluable in giving me the confidence to get started.
I have already started to make changes to my wiring diagrams as a result of the training (diagram structure, wire labelling conventions, etc) which will give me a much more functional diagram that I can more easily map to the physical layout in my airplane.
The class was also a great opportunity to network with other builders. A local Garmin rep for experimental visited on day 2 and 3. Decals for all of the G3X panel-mount components were provided to help with panel layout (plus other swag).
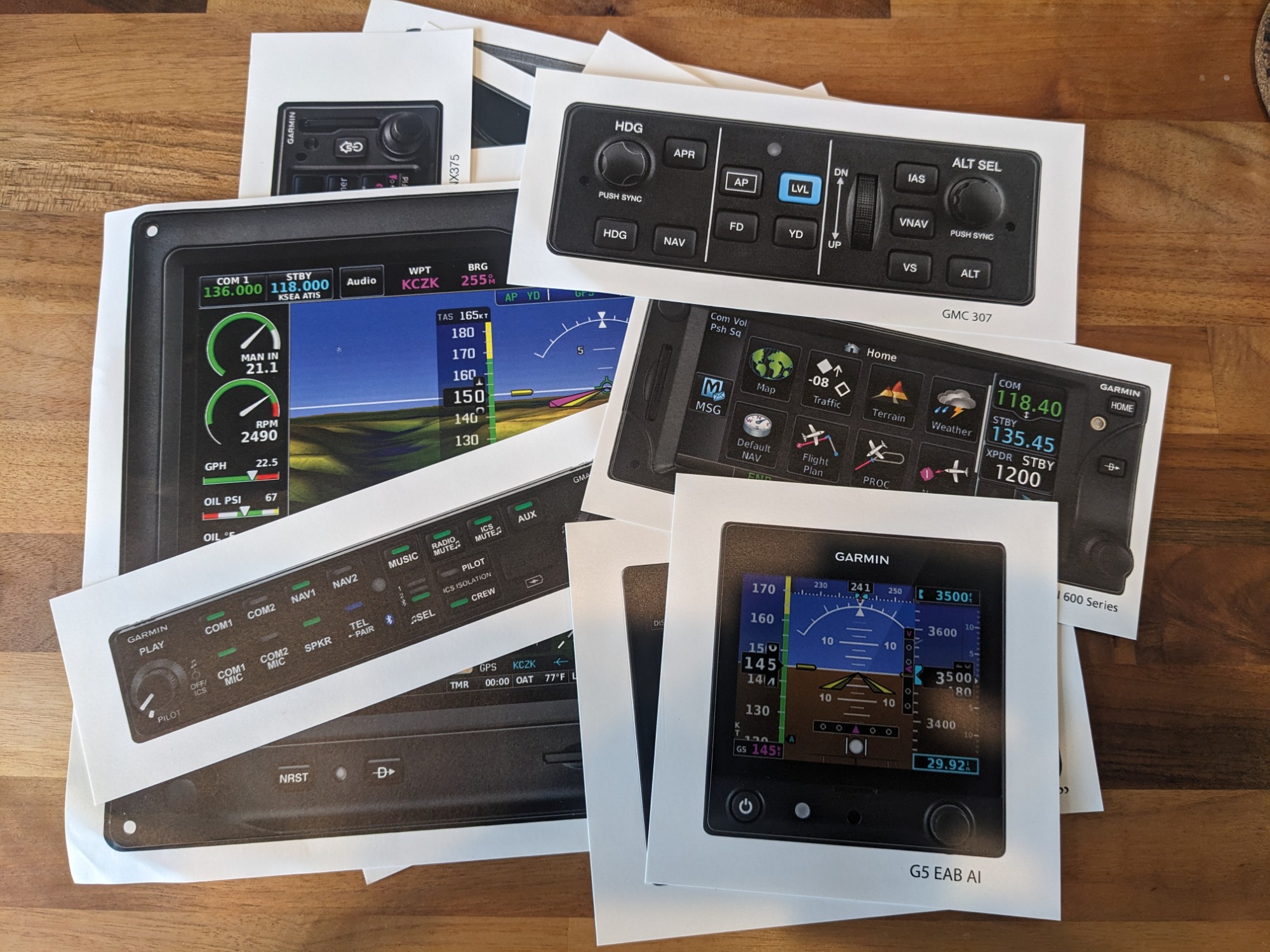
The Garmin rep provided a walkthrough of the G3X system planning/pricing worksheet and discussed various component combinations for different missions. He is also building an RV-10 so we got to commiserate on the doors. Speaking of which, I need to get back to those..